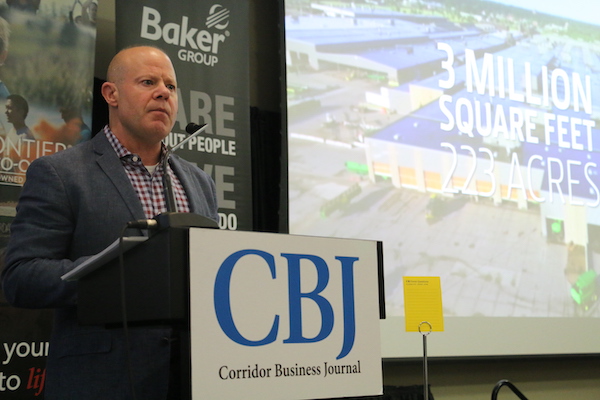
The ongoing transformation to Industry 4.0, or smart manufacturing processes, depends in large measure to not only gathering vital data, but implementing it in practical and useful ways, keynote speaker James Leach said Sept. 15 during a keynote address at the Corridor Business Journal’s annual Manufacturing Conference at the Hotel at Kirkwood Center in Cedar […]
Want to Read More?
Get immediate, unlimited access to all subscriber content and much more.
Learn more in our subscriber FAQ.
- Unparalleled business coverage of the Iowa City / Cedar Rapids corridor.
- Immediate access to subscriber-only content on our website.
- 26 issues per year delivered digitally, in print or both.
- Support locally owned and operated journalism.
Do you want to read and share this article without a paywall?
Click here to purchase a paywall bypass linkThe ongoing transformation to Industry 4.0, or smart manufacturing processes, depends in large measure to not only gathering vital data, but implementing it in practical and useful ways, keynote speaker James Leach said Sept. 15 during a keynote address at the Corridor Business Journal’s annual Manufacturing Conference at the Hotel at Kirkwood Center in Cedar Rapids.
Mr. Leach, factory manager at the John Deere Harvester Works in East Moline, Illinois, noted that the operation has existed in some form since 1912, and currently comprises an estimated 3 million square feet of factory space under roof on a 90-acre site, employing 2,500 workers in a complex, multi-shift production system.
As a market leader, John Deere is expected to deliver exceptional product solutions to their domestic and international customers, Mr. Leach said.
“Our value proposition is not that we're going to be a price fighter,” he said. “We're going to sit at the top of the market for most of our product offerings. So we have to deliver on value that extends throughout the lifecycle of those machines and delivers real economic value for our customers, and then we need to bring some of that same innovation ethic into our factories to make sure that we can continue to live and work in these communities, to have factories like Waterloo and Harvester Works and Davenport Works that help ensure that we can thrive.”
Mr. Leach pointed out that depending on configuration, customers for the company’s latest Series X combines “are going to be spending over $1 million on that harvesting solution. So it has to be bulletproof, it has to be on time, and it has to be right, or we put our business at risk.”
The X Series product line, launched in 2020, features a host of industry-leading technologies, Mr. Leach said, from onboard machine learning, multiple cameras to monitor operation, automated grain sampling sensors and a host of other features that have allowed Deere to compete head to head with “a competitor up in Canada and allow us to take share from them. So we’re really bullish on the future of our new product programs.”
However, that level of technical innovation includes substantial complexity in manufacturing processes. Mr. Leach noted that Harvester Works has about 30,000 active part numbers in its factory, aggregating a host of systems into a cohesive end product.
“It really is that value proposition, that we're going to marry the very best piece of equipment to a top-flight combine,” he said. “And we're going to provide economic headroom to our customers because of the product offering that we can put together in a unique way that will go out and allow them to harvest almost in any condition, and do it as efficiently and as profitably as possible.”
The best solutions, Mr. Leach said, are those that can be delivered to customers as they’re using the equipment in their own operations.
“We really think there's a future where we're able to monetize conditions-based monitoring of a machine in the field where you can overlay all kinds of different parameters, be it moisture in the ground, UV or wind,” he said. “When you think of all the different things that a farmer has to deal with, we can provide a solution for them. We can digitize that solution, send it to their machine in the field and optimize their configuration, and also be able to predict when there's going to be downtime.”
At John Deere Harvester Works, manufacturing innovation depends on the efficient integration of technical and mechanical processes, Mr. Leach said.
“When we talk about innovation, it’s really about how we make sure that our human capital and the capital we spend intersect at the right place using digital tools,” he said, “so we can try to advance our ability toward prediction, using machine learning and upskilling our workforce so that we make sure that we're driving competitive advantage to the bottom line, and also how that extends out to our wage workforce and how we can enable them to be more successful.”
Efficient workforce training is key for Harvester Works, Mr. Leach said, and became especially critical during the COVID-19 pandemic, when John Deere’s operations grew dramatically, requiring the hiring of hundreds of new workers in a compressed time frame.
“We took a survey of all those who came in,” he said. “Most had been in the services industry, some of them were fresh high school graduates. And now we were handing them a torque tool and saying ‘go build this million dollar solution for our customers.’ There's going to need to be something other than those traditional written operating methods, with sheets in a binder that they never look at. You're going to have to do something different if you’re going to drive the same level of quality and higher level of productivity while you're introducing new machines, new parts and (processes) at the same time.”
The pace of technological changes in manufacturing is accelerating as the era of machine learning and artificial intelligence nears, Mr. Leach said.
“Like Moore's law, it compresses over time, so as we're entering into industry 4.0, it will be really interesting to see what happens with additive manufacturing, as well as generative AI and where that takes us in the future, because it's coming,” he said. “We've got some novel use cases at Harvester Works. We're introducing large language models into our data streams, seeing if we can unlock innovation and also unlock greater efficiency, especially for our manufacturing engineers, seeing if there are ways we can take our historical information and leverage that in a way that we can offer those things and just have the human check, to make sure that the sequence of events is correct.”
One of Harvester Works’ goals, Mr. Leach said, is to minimize “technical debt” by creating convergence on a common tech stack, rather than creating proprietary processes that may become obsolete and require a whole new set of processes.
“We call those execution circles,” he said. “We're trying to build this thread across all of our manufacturing facilities. The optimal outcome is that of a digital twin, both of your facility and of the machines.”
Harvester Works is also pursuing automation of certain repetitive tasks, including parts retrieval and visual inspection of mechanical components during assembly — autonomous mobile robots, for example, to optimize inventory accuracy and handle other mundane tasks — which can be combined with high-end human oversight.
“We've got people who are writing code, generating new solutions, and making our machines the most advanced in the world for what they do,” he said. “We need to bring that same type of pioneering innovation inside our manufacturing locations, and we don't want to get left behind. But the other thing you don't want to do is just light up the factory, put sensors everywhere and not do anything with the information. So it's got to be actual information that drops to the bottom. And that's really what we've been trying to do, not just have more blinking lights out there, not just have more information that sits in a data table that nobody ever looks at. How do you bring that inside of the factory into the leadership team and really intentionally drive the use of that information to answer questions?”
Redeployment of employees that were formerly performing repetitive tasks can lead to a return on investment in as little as six months, Mr. Leach said.
“It’s that work smarter, not harder mindset,” he said. ”If we can find digital solutions to improve our personal productivity, and get out of some of that non-value added work that are the traps that we all fall into — that's a real value statement for the team, and it's really accelerating adoption.”
As the pace of innovation accelerates, however, it’s critical that employees understand and support the changes, including potential benefits, Mr. Leach said.
“You've got to work through acceptance with the wage employees on the shop floor,” he said. “Every two weeks, we've got a standing committee meeting with myself, labor relations, the shop committee chair and my leader for innovation, where we're trying to get in front of the next use case … We also have an incentive program with our Deere UAW factories, where we can use these productivity enhancements to help our employees protect their earnings over time, and then they can continue to be earning premium wages inside of their factories and not have that decline over time, especially in inflationary periods like this.
“Really, it’s all about people,” he added. “We're a long way from being a lights-out combine factory, where I just hit a button and the combine comes out the other side. You have to bring people along on your digital journey, because we don't want to create new robots that are afraid of machines. We need to bring these solutions into our factories, deploy them, harden them and really sell the value proposition, so we can maintain our manufacturing operations here in the Midwest."